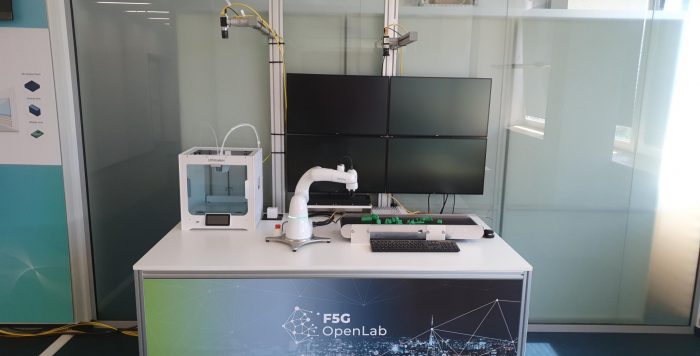
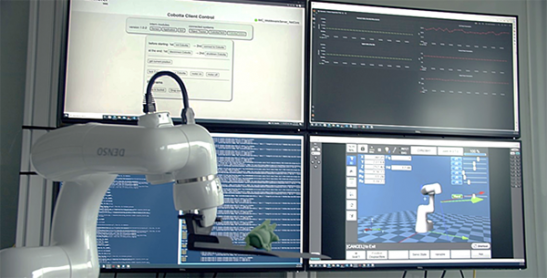
This interactive PoC demonstration presents an AI-based vision analysis, implemented on an edge cloud for a visual inspection scenario of additive manufactured artefacts in production processes. As such, the PoC focuses on demonstration of different features such as an end-to-end manufacture control loop, comprising an industrial camera – edge cloud – robot arm, connectivity between all these components via a passive optical network (PON), including fiber-to-the-camera and fiber-to-the-robot, and an AI-based video analytics/vision analysis of customizable 3D-prints on the edge cloud consisting of a full video-edge-robot pipeline.
As a result, a general low-latency ML-based video processing-pipeline will be implemented to access video data from the demo environment as fast, as detailed, and as reliable as possible. A middleware interface will be also implemented to communicate real-time information between the video processing components, the robot actuators and a user interface. The software will be first developed and tested in our lab setting using video-recorded training data, then tested iteratively, followed by the integration into the final interactive demo use case within the F5G OpenLab at Fraunhofer HHI. As a result, the object detection and inspection video application components will be integrated into the demo setup.
PoC Team Members: Fraunhofer HHI, Denso Robotics, German Edge Cloud, Huawei